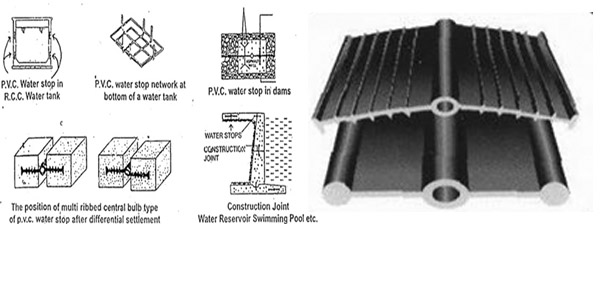
In many cases concrete structure are only as watertight as the waterstops used in them. Installed in expansion joints, cold joints and other seams they are available in vide variety of shapes and types, Concrete like all material, expands and contract when the tempreture fluctuation, To accommodate that changes expansion joint are installed at regular intervals throught the walls and slabs and if the expansion joint aren't installed properly the structure will crack along with natural weal points. That's w hy nearly all large scale concrete structure –water treartments plants, dams usually have WATERSTOPS INSTALLED, during construction, residential jobs sometimes use waterstops as well, but usually only at cold jointbetween footer and foundation.
Sr No | TEST | Required As per IS:12200 Of 1987 | Required As per IS:15058 of 2002 | Required As per ASTM | Observed Value of Manpower PVC-WATERSTOP |
1 | Tensile Strength (Kg/Cm²) | 116.0 min. | 138.0 min. | 122.50 min. | 155.00 |
2 | Ultimate Elongation ( % ) | 300.0 min. | 285.0 min. | 350.00 min. | 375.00 |
3 | Tear Resistance (Kg/Cm²) | 49.0 min. | 49.0 min. | 19.25 min. | 57.00 |
4 | Hardness ( Shore A ) | 65.0 min. | 65.0 min. | 65.00 min. | 70.00 |
5 | Water Absorption ( % ) | N.A. | 0.6 max. | N.A. | 00.02 |
6 | Cold Bend Test at -25ºC | N.A. | No Cracking | N.A. | No Cracking |
7 | Accelerated Extraction at 14th Day a) Tensile Strength (Kg/Cm²) b) Ultimate Elongation ( % ) |
105.0 min. 250.0 min. |
103.0 min. 280.0 min. |
105.0 min. 250.0 min. |
125.00 298.00 |
8 | Stability Effect of Alkali a)Weight Increase at 7th day ( % ) b)Weight Decrease at 7th day( % ) c)Change in Hardness at 7 day d)Weight Increase at 28th day ( % ) e)Weight Decrease at 28th day( % ) f)Dimension Change ( % ) |
0.10 max. 0.10 max. ± 5 0.40 max. 0.30 max. ± 1 |
0.25 max. 0.10 max. ± 5 0.40 max. 0.30 max. ± 1 |
0.25 max. 0.10 max. ± 5 0.40 max. 0.30 max. ± 1 |
0.07 - + 1 0.08 - + 1 |
Our company has gained immense recognition in this domain for manufacturing and presenting an excellent assortment of Hydrophilic Swell Bar. These rubber sheet are made as per the laid down rules & regulations of the industry. Our offered range of hydrophillic sheet is used for sealing of joints in underground prec ast elements, tunnels, vertical construction joints and concrete-steel joints. Swell Bar is known for its characteristics such as water proof quality, resistance to weather and excellent durability.
Technical Data
ETHYLENE PROPYLENE DIENE MONOMER (EPDM)sheets are extensively used for protection of liquid contamination, agricultural,Industry, industrial projects. EPDM Sheet acts as a perfect line to prevent foreign material entering through ground water source as well as prevent seepage loss in water conservation projects. Our Speciality Colorfull Membrane for Water Proffing.
Other Applications: • Lining of industrial effluent plant, Tunnels & Underground Works
• Packaging and wrapping, Water proofing for terrace gardens
• For protection of food grains, fertilizers, cotton, chemicals, Cement, constructions and power plants & Steel Plants Etc. Concrete road and bridge
Properties of EPDM: • Mans EPDM Sheet has excellent mechanical properties.
• Saves water seepage upto 80% of total quality of water
Available.
• It has a very low moisture/vapour transmission rate.
• Very good resistance against chemical and unaffected by Bacterial or fungal growth.
• Very good resistance against ozone, oxidation, weather & water because polyethylene has a long chain of hydrocarbon which gives above properties.
Unsupported flexible Poly Vinyl Chloride membrane is manufactured from polymer of vinyl chloride such material compounded with plasticizer, stabilizer and then converted in to flexible sheet.
UPVC Water proofing membrane is necessary in all the area starting from small household to large building included the biggest industrial and the commercial building needs reliable membrane that the dryness of the concrete, masonry membrane structure and make it safe against the attack from salts, alkalis and from certain acids and provides water and weather resistance.
USES 1. SWIMMING POOL
2. TANKS
3. RESERVOIRS
4. HYDRO PROJECTS
5. FOUNDATION AND UNDERGROUND WORK
6. TUNNELS
7. ROOF DECK GARDENS
S.NO. | Properties | Unit | Type |
1 | Thickness | mm | 0.26 to 2 mm |
2 | Tensile Strength | Kgf/cm² | 120 min. |
3 | Elongation at Break | % | 150 min. |
4 | Tear Strength longitudinal and | Kg/cm | 40 min. |
5 | Cold Resistance at 0°C x 1hour | Visual | No Crack |
6 | Ageing resistance | Excellent | Excellent |
7 | Water resistance | Excellent | Excellent |
8 | Bacteria resistance | Excellent | Excellent |
9 | Soil Chemicals resistance | Excellent | Excellent |
MAN APP is a granule surfaced APP modified bitumen membrane. It consists of select asphalt, modified with atactic polpropylene, and reinforced with a non-woven 190 g/m² (3.9lb/100ft²) polyester mat enhanced with continuous glass fiber strands in the machine direction. The combination results in a flexible, yet durable roofing membrane that exceeds the performance requirements of ASTM D 6222 Type I, Grade G.
MAN APP membranes are ideal for both new construction and re-roofing application as a base ply, cap sheet, or as a flashing sheet in multi-ply applications. Low slop roofs of any size, even those with numerous penetrations, may accommodate a MAN APP membrane application.
Method of Application:
1. All floor area shall be cleaned to make it free from dirt , dust and other contaminants.
2. All surface shall be primed using bituminous based primer with good quality of roller / brush and allowed to dry completely to assured bond with the prime surface and elimination of air bubbles.
3. Install a layer of 3mm thick MAN APP membrane , over the RCC floor surface from the lowest point to enable laps to shed water. all the edge and end laps must be overlapped minimum of 100mm. all end laps and exposed edges shall be sealed using tourch.
Storage:
1. All material should be stored out of the weather in a clean, dry area in its original at a minimum of 50°F(10°C) and a maximum of 100°F (38°C) or above at the time of application.
2. If material must be stored temporarily on the roof before application, it must be elevated from the roof surface on a pallet, stored on end, and covered from the weather with a light colored opaque tarp in a neat, safe manner that dose not exceed the allowable load limit of the storage area.
Precautions:
1. Take care when transporting and handiling MAN APP rolls to avoid punctures and other types of damage.
2. Isolate waste products, petroleum products, grease, oil (mineral and vegetable) and animal fats from all MAN APP membranes
ASTM D 6222 Type I, Grade G:
Physical Properties Tested with ASTM D 6222 | ASTM Standard Reqd Value | Units | MAN’S Value | Metric Unit | MAN's Value |
Product Thickness | 103 | mil | 119 | mm | 3 |
Net Mass | 60 | Lb/100ft² | 80 | g/m² | 3900 |
Bottom Side Coatig | 30 | mil | 48 | mm | 1.2 |
Peak Load @ 0°F (-18°C) | 60 | lbf/inch, MD | 120 | kN/m | 21 |
Elongation @ Peak Load @ 0°F (18°C) | 10 10 |
% MD % CD |
24 29 |
% % |
24 29 |
Peak Load @ 73°F (25°C) | 50 50 |
lbf/inch, MD lbf/inch, CD |
90 80 |
kN/m kN/m |
21 16 |
Elongation @ Peak Load @ 73°F (25°C) | 23 23 |
% MD % CD |
42 51 |
% %/td> | 42 51 |
Ultimate Elongation @5% of peak load 73°F (25°C) | 30 30 |
% MD % CD |
45 57 |
% % |
45 57 |
Tear Strength @ 73°F (25°C) | 70 70 |
lbf, MD lbf, CD |
90 120 |
N N |
400 534 |
Dimensional Stability | 1 1 |
% change MD % change CD |
-0.05 0.04 |
% % |
-0.05 0.04 |
Low Temperature Flexibility Compound Stability | 0 230 |
°F °F |
14 270 |
°C °C |
-10 132 |